About 70% of the world’s oil and gas is found in deepwater areas. This makes deep offshore tech very important for energy. Thanks to subsea engineering, we can now explore and use these resources. This is helping build offshore structures.
As energy needs keep rising, deep offshore tech becomes even more vital. It’s changing how we get energy, with subsea engineering at the heart. New tech and methods have made deepwater work more efficient and cheaper.
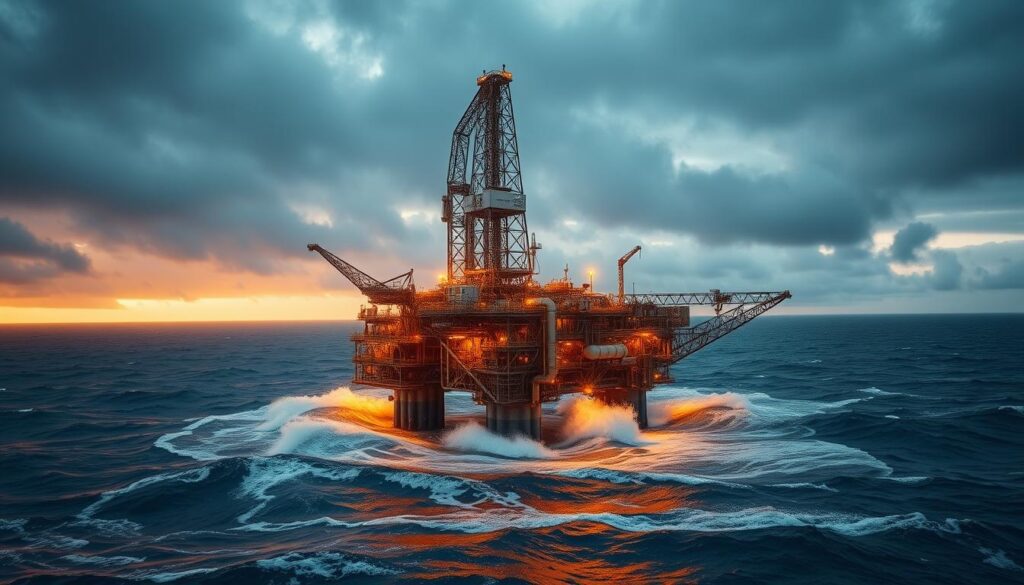
Key Takeaways
- Deep offshore technology is essential for accessing remaining oil and gas reserves
- Subsea engineering is critical for the development of offshore infrastructure
- Advances in deep offshore technology have improved efficiency and reduced costs
- Offshore infrastructure is a key component of deepwater operations
- Deep offshore technology is driving the growth of the energy sector
- Subsea engineering and offshore infrastructure are closely linked
Understanding Deep Offshore Technology Fundamentals
Deepwater drilling and offshore production systems are key in the oil and gas world. As energy demand rises, so does the need for deepwater operations. It’s vital to grasp the basics of deep offshore tech for safe and efficient resource extraction.
Offshore systems include platforms, rigs, and pipelines. These are built to last in tough marine settings. They must be safe and strong. Important tech needs include subsea processing and working at great depths.
Core Components of Offshore Systems
- Platforms: used for drilling and production operations
- Rigs: used for drilling and exploration
- Pipelines: used for transporting resources to shore
Protecting the marine environment is a big deal in deepwater work. The industry must design and run offshore production systems to harm the sea less. This means stopping oil spills and keeping marine life safe.
Key Technical Requirements
Deepwater work needs to handle extreme depths and harsh seas. Subsea processing is key. It lets resources be processed underwater, cutting down on surface needs.
Essential Equipment for Deepwater Operations
Exploring the deep sea needs special equipment that can handle its harsh conditions. Underwater robotics are key for safety, efficiency, and exploring deeper waters. Some vital tools for deepwater work include:
- Remotely Operated Vehicles (ROVs) for inspection and maintenance
- Autonomous Underwater Vehicles (AUVs) for surveying and mapping
- Subsea production systems for oil and gas extraction
These technologies are vital for deepwater exploration and work. They help companies get and use resources from the deep sea. The use of underwater robotics has grown a lot, thanks to better design, materials, and sensors.
Other important tools like subsea pumps, valves, and pipelines are also needed. These advancements have let the oil and gas industry reach deeper waters. This has opened up new resources and reserves.
Advanced Subsea Processing Systems
Subsea engineering is key in offshore energy development. It makes it possible to process and treat hydrocarbons under the sea. Advanced systems use the latest tech to separate, compress, and move hydrocarbons.
These systems are vital for offshore energy. They help separate oil, gas, and water efficiently. They also compress gas for long-distance transport. Subsea engineers design these systems, facing the unique challenges of the sea.
Separation Technologies
Separation tech is a big part of these systems. It separates oil, gas, and water well. Advanced membranes and filters are used, built to handle the sea’s harsh conditions.
Compression Systems
Compression systems are also crucial. They make it possible to move gas far away. Advanced compressors and pumps are used to compress the gas, sending it to processing facilities.
Flow Assurance Solutions
Flow assurance solutions are key too. They stop hydrates and wax from blocking pipelines. Advanced chemicals and tech are used to prevent these issues, keeping the system running smoothly.
With these advanced technologies, subsea processing systems help produce hydrocarbons safely and efficiently. They also reduce the environmental impact of offshore energy. As energy demand grows, so will the role of subsea engineering and these systems.

Implementing Underwater Robotics in Offshore Operations
Underwater robotics is changing the offshore industry. It makes tasks like inspection, maintenance, and repair safer, more efficient, and cheaper. It’s becoming key in offshore production systems.
Using underwater robotics in offshore work has many benefits. It includes enhanced safety, less downtime, and better data collection. For instance, Remotely Operated Vehicles (ROVs) help check and fix offshore gear. This lowers accident risks and boosts efficiency.
Some main uses of underwater robotics in offshore work are:
- Inspection and maintenance of offshore equipment
- Repair and replacement of damaged equipment
- Data collection and monitoring of offshore operations
Adding underwater robotics to offshore work makes operations safer and more efficient. It also cuts costs. As the offshore sector grows, underwater robotics will be crucial in shaping its future.
Application | Benefits |
---|---|
Inspection and maintenance | Reduced downtime, improved safety |
Repair and replacement | Cost savings, improved efficiency |
Data collection and monitoring | Improved decision-making, reduced risk |
Smart Integration of Offshore Production Systems
The offshore industry is changing fast. It’s using new technologies to work better, spend less, and stay safe. This change is big in offshore infrastructure and deepwater exploration. Digital solutions help companies work smarter, be more efficient, and make better choices.
Digital twin technology is key to this change. It makes virtual copies of offshore assets. This lets companies watch them in real time, fix problems before they start, and work at their best. Remote monitoring is also important. It lets operators control their assets from one place. Plus, using data analytics helps spot trends, find oddities, and make choices based on facts.
- Improved operational efficiency
- Enhanced safety and reduced risk
- Increased production and revenue
- Better decision-making through data analytics
The offshore industry will keep growing, and smart tech will be essential to keep up. By using digital twin tech, remote monitoring, and data analytics, companies can find new ways to grow and succeed in deepwater exploration and offshore infrastructure.
Technology | Benefits |
---|---|
Digital Twin Technology | Predictive maintenance, optimized performance |
Remote Monitoring Solutions | Real-time monitoring, centralized control |
Data Analytics Implementation | Data-driven decision-making, trend identification |
Maximizing Efficiency in Deepwater Exploration
To boost efficiency in deepwater exploration, it’s key to use smart strategies and tech. Deepwater drilling can be made better with subsea processing systems. These systems help separate and treat hydrocarbons right on the seafloor.
Improving deepwater exploration involves several steps:
- Optimized drilling practices to reduce time and costs
- Implementation of subsea processing systems to enhance hydrocarbon recovery
- Use of data analytics to inform decision-making and optimize operations
By combining these methods, operators can see better results. For instance, deepwater drilling can get more efficient with real-time data analytics. This helps adjust drilling parameters, saving time and money.
Also, subsea processing systems can lessen environmental harm. They reduce hydrocarbon releases into the ocean. By using these strategies, operators can make deepwater exploration more efficient and successful.
Maximizing efficiency in deepwater exploration needs advanced tech, smart operations, and data-driven choices. These steps help cut costs, improve safety, and reduce environmental harm. This way, operators can achieve more in their deepwater projects.
Strategy | Benefits |
---|---|
Optimized drilling practices | Reduced time and costs |
Subsea processing systems | Enhanced hydrocarbon recovery |
Data analytics | Improved decision-making and optimized operations |
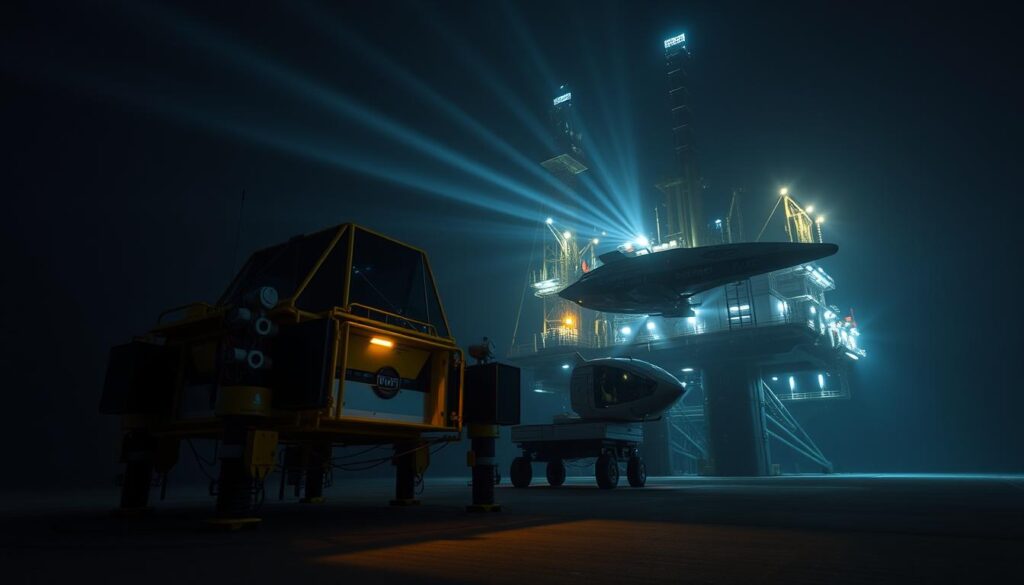
Safety Protocols and Risk Management Strategies
Safety and risk management are key in offshore energy development. The deep offshore technology field is risky due to high-pressure systems and harsh weather. Companies must have strong safety plans and emergency systems to manage these risks.
Important steps include regular maintenance of equipment, thorough training of workers, and continuous monitoring of operations. This focus on safety helps prevent accidents and meets regulatory standards.
Emergency Response Systems
Good emergency response systems are vital for handling accidents. They should include
- Emergency response plans
- Regular drills and training
- Communication protocols
Environmental Protection Measures
Protecting the environment is crucial to avoid pollution and harm to marine life. Companies must take steps to prevent oil spills, reduce waste, and minimize habitat disruption. This approach helps reduce environmental impact and follows legal rules.
By following these safety and risk management steps, companies can develop offshore energy safely and responsibly. This ensures the use of deep offshore technology is done right.
Also read: Unlock the ZeV Technology for Your Business
Conclusion: Embracing the Future of Offshore Technology
The future of deep offshore technology is bright. New breakthroughs in subsea engineering will open up new areas. This will help us use energy resources in a safe and green way.
There are many challenges ahead. But with creative ideas and teamwork, we can overcome them. This will lead to exciting changes in our industry.
New tech like digital twins and remote monitoring will change how we work. It will make our operations safer and better for the planet. Robots and underwater vehicles will also make exploring and fixing underwater easier and more precise.
As the world’s energy needs grow, deep offshore tech will be key. By moving forward, we can create a better future. This future will bring economic growth, protect our environment, and showcase our technological skills.
FAQ
What are the core components of offshore systems?
Offshore systems have platforms, rigs, and pipelines at their core. These are built to handle the deep sea’s harsh conditions. They help in exploring, extracting, and moving resources.
What are the key technical requirements for deep offshore operations?
Deep offshore work needs special gear and tech. This includes stuff that can handle high pressure, extreme cold, and corrosive environments. Advanced materials, special sensors, and strong control systems are key for safety and efficiency.
What environmental considerations are important for deep offshore technology?
Protecting the environment is vital for deep offshore tech. It’s about stopping oil spills, lessening marine ecosystem harm, and proper waste disposal. Using green energy and subsea processing systems helps reduce environmental impact.
What is the role of underwater robotics in deep offshore operations?
Underwater robots, like ROVs and AUVs, are crucial for deep offshore work. They make inspections, maintenance, and repairs safer and more efficient. They also aid in exploration and data gathering in deep waters.
How are advanced subsea processing systems improving offshore operations?
New subsea processing systems are making offshore work better and greener. They help separate oil, gas, and water efficiently. They also transport gas far and prevent problems like hydrates and wax. Subsea engineers lead in designing these systems for offshore energy.
What is the role of digital twin technology in offshore production systems?
Digital twin tech is changing offshore system management. It creates virtual copies of assets for real-time monitoring and predictive maintenance. This mix of digital and physical systems boosts efficiency, safety, and sustainability in offshore work.
What are the key safety protocols and risk management strategies in deep offshore technology?
Safety and risk management are top priorities in deep offshore tech. This includes having strong emergency plans, protecting the environment, and following rules. A proactive safety approach is key to managing risks and ensuring the industry’s future.